- نمونه کار عربی کشور عراق
- کارتن میوه و صیفی جات
- جعبه و کارتن خرما
- جعبه و کارتن بسته بندی خشکبار
- لوازم الکتریکی و الکترونیکی
- جعبه و کارتن لوازم خانگی
- بسته بندی مواد غذایی
- جعبه بسته بندی غذا و فست فود
- بسته بندی لوازم آرایشی بهداشتی
- جعبه قطعات صنعتی و مکانیکی
- جعبه اسباب بازی
- جعبه و کارتن ظروف
- بسته بندی تجهیزات پزشکی
- جعبه بسته بندی عطر و ادکلن
- کارتن اسباب کشی
- جعبه و کارتن زغال
- کارتن بسته بندی ساعت
- سایر نمونه کارها
- همه نمونه کارها
تاثیرات طراحی و ساخت کلیشه در چاپ کارتن بسته بندی
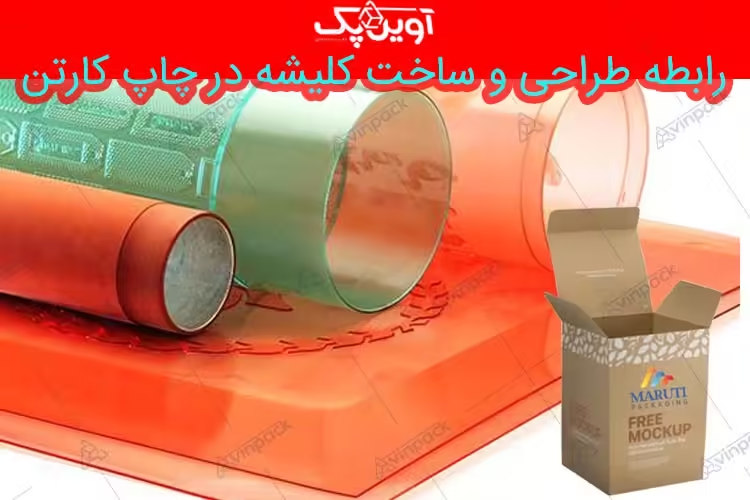
آخرین ویرایش اسفند 8, 1403
تاثیرات طراحی و ساخت کلیشه در چاپ کارتن بسته بندی موضوع اصلی این مقاله است. در این محتوا به اهمیت طراحی کلیشه برای چاپ طرح گرافیکی روی کارتن بسته بندی پرداخته شد است. صفر تا صد کارتن سازی با چاپ فکسوگرافی به همراه جزییات بسیار کاربردی در این مقاله گرد هم آمده است. این نوشته مناسب است برای تولید کننده گان کارتن و همچنین سفارش دهندگان کارتن، تا بهترین کیفیت به مشتریان و خود و بازار ارائه دهند.
روشهای گوناگونی در خصوص چاپ روی کارتون ابداع شده است که میتوان از چاپ دیجیتال، سیلک اسکرین، افست (که پس از چاپ روی مقوا (پوستر) بر روی کارتن چسبانده میشود) و چاپ فلکسوگرافی نام برد. چاپ فلکسوگرافی نخستین بار با نام چاپ آنیلاین و در سال ۱۸۹۰ در کشور انگلستان اختراع شد و اسم خود را از روغن آنیلاین در مرکب چاپ گرفته است. تا سال ۱۹۵۱ این شیوه با بیش از ۲۰۰ نام مختلف شناخته میشد و نهایتا در سال ۱۹۵۲ این روش با نام فلکسوگرافی تا به امروز نام گذاری شد.
نگاهی کوتاه به چاپ فلکسو گرافی
چاپ فلکسوگرافی از فن آوری چاپ برجسته بهره گرفته است ویژگی اصلی چاپ فلکسیوگرافی استفاده از فرمهای چاپ منعطف است که قادر به تغذیه مرکب خاصی به اسم ویسکوزیته پایین، هستند. کلیشه کارتن جزء یکی از ابزارهای چاپ بوده و درفلکسوگرافی از لاستیک و یا فتوپلیمر ساخته میشود که سختی و ضخامت آنها بر اساس سطح چاپی و نقوش مورد نظر ما تعیین و انتخاب میشود که برای چاپ کارتون معمولاً از کلیشههای با قطرهای مختلف بسته به نوع دستگاه و نوع چاپ استفاده میشود.
چاپ فلکسوگرافی یکی از متداولترین و مقرون به صرفهترین چاپها برای تیراژها و اندازههای مختلف بر روی کارتون میباشد که در آن عمل چاپ بر روی کارتن توسط کلیشه انجام میشود. عوامل موثری چون تاثیرات طراحی، تاثیرات کشانی در چاپ، نقش نوردهی در ساخت کلیشه و تاثیر شستشو در کیفیت ساخت آن، تاثیرات شور (درجه سختی) کلیشه در کیفیت چاپ، نحوه ی برش کلیشه و طریقه مونتاژ آن، نحوه نصب کلیشه بر روی سیلندر چاپ و طریقه تمیز کردن آن، نگهداری و بایگانی کردن کلیشه، حائز اهمیت است.
ضخامت کلیشههای فلکسوگرافی
در چاپ فلکسو، کلیشههای نازک با برجستگی کم عمق، جزئیات را به خوبی ایجاد مینمایند ولی همواره به سطحی خیلی تمیز و عاری از خاک کاغذ و مقوا احتیاج دارند. ضخامت کلیشه خیلی مهم است زیرا باید به دور سیلندر چاپ کشیده شود و بعد از نصب بر روی سیلندر، قسمت بیرونی کلیشه بلندتر از قسمت درونی آن میشود و هرچه کلیشه ضخیمتر باشد اختلاف دو سمت کلیشه بیشتر میگردد.
مرحله و عوامل تاثیرگذار در طرح یک کارتون
طراحی جعبه مقوایی نقش مهمی در بازاریابی محصول ایفا میکند که سه نکته اساسی در آن مورد توجه میباشد:
- زیبایی شناسی ظاهری
- قابلیت استفاده مناسب و ایجاد لذت در استفاده
- واکنش های که ایجاد میکند از قبیل بازتابهای اجتماعی و تاثیرات شخصی
بستهبندی کارتن علاوه بر، برآوردن نیازهای بازاریابی و تبلیغات انتظارات زیر را نیز تامین کند:
نکات مهمی که در طراحی کارتن باید به آن ها توجه نمود عبارتند از:
- گنجاندن و محافظت کردن از محصول
- قابلیت استفاده (کارکرد مناسب)
- متمایل جلوه دادن محصول در قفسه فروشگاه
- برانگیختن احساسات خریداران
- در نظر گرفتن نوع و خصوصیات محصولات شامل ابعاد، آحاد، وزن و شکل
- روش ساخت مانند محلهای اتصال و مواد مصرفی در اتصالات، شیوه صحیح اتصال ها
- دوام و طول مدت نگهداری به خصوص در بستههای مواد غذایی، مهمات و صنایع نظامی
- نوع و نحوه چیدمان (چیدمان با ارتفاع زیاد، بستهبندیهای محکم تری را میطلبد)
- در نظر گرفتن محل تهویه (برای محصولات سردخانهای)
- تطبیق خصوصیات و طرح بسته با استانداردهای حمل و نقل
- محلهایی درب (پایین بالا پهلو) و نحوه باز شدن
- زیرسازی و استحکام با توجه به توزیع بار در کف آنها و توجه به ضربهگیرها
- زمان لازم جهت بستهبندی یا مونتاژ برای سفارشهای دایکاتی
- استحکام کافی در مقابل عوامل مختلف فیزیکی، شیمیایی و به ویژه مکانیکی
- حفظ کیفیت و ارزش محصول با در نظر گرفتن سازگاری مواد با محصول
- تقسیم بندی درون بسته برای محصولات چند تکه یا بستهبندی گروهی
- در نظر گرفتن محل برچسب طراحی گرافیک بر روی بسته و انتقال اطلاعات مناسب در مورد باز کردن نحوه استفاده و تاریخ مصرف یا انقضا و مواردی از این دست.
اقتصادی بودن طرح با توجه به امکانات مشتری
برای موفقیت در چاپ به طراح تخصصی چاپ کارتن نیاز داریم و شایسته است از وسعت اطلاعات خوبی برخوردار باشد و به ویژه از نوع دستگاه چاپ کارتون (از قبیل نوع آنیلوکس، درصد کشانی سیلندر چاپ، سرعت ماشین، نوع ورق کارتن برای چاپ، گرماژ کاغذ مورد استفاده برای چاپ و …)
با توجه به اینکه در چند سال اخیر تحولی در چاپ کارتن به وجود آمده است میتوان انواع طرحهای چاپی که در صنعت چاپ کارتون مورد استفاده قرار میگیرد را به موارد زیر تقسیم کرد:
- خطی (Line art) : طرحی است شامل انواع حروف (type)، خط (Line)، و یا تنپلات (solids)
- ترامه (screen art) : طرحی است تک رنگ یا چند رنگ تفکیکی که از کنار هم قرار گرفتن ترام ۲ یا چند رنگ، رنگ دلخواه شکل میگیرد.
- ترامه تصویری (process) : که به روش تفکیک رنگ و به صورت فیلمهای جداگانه برای چهار رنگ تهیه میشوند که میتوان چاپ هافتون را به این روش تهیه میشود را نام برد.
طرح گرافیکی
در مرحله طراحی توجه به نکات زیر در بالا بردن کیفیت چاپ در کارتون موثر میباشد:
- باید کلیه متنها و تصاویر از حجم یکسانی برخوردار باشند تا در تفکیک دچار افت کیفیت نباشند.
- متن نباید خیلی ریز باشد زیرا در چاپ موجب پرشدگی یا بولى شىن میشود.
- متن نباید به صورت خیلی نزدیک حروف چینی شود و حداقل فاصله بین حروف 1.5 mm باشد.
- با توجه به خطوط ظریف، ضروری است تا بیش از اندازه نازک نشود.
- برای خطوطی که تک رنگ میباشد و به صورت خطهای توپر (positive rule)نباید کمتر از 0.15 mm باشد.
- برای خطوطی که تک رنگ میباشد و به صورت های خط های توخالی اند (Reverse rule) نباید کمتر از 0.2 mm باشد.
- باید توجه به داشت تلرانس چاپ در کار های چند رنگ و به خصوص هافتون در حدود 0.4 mm میباشد که باید در اندازه ترامها و یا خطوط دقت کرد.
- بازتابش ترام های اوربیتال باید به صورت واضح و شفاف کپی شود و کاهش طول، که به خاطر کشیدگی چاپ از اهمیت زیادی برخوردار است، بهتر است در صورت امکان قبل از چاپ و تولید نگاتیو انجام شود و طرح مورد نظر با استفاده از نرمافزارها گرافیکی از یک سمت کوچک شود و برای مراحل بعدی ارسال گردد.
- خطوط دور کادر بهتر است به اندازه کافی پهن باشند و به رنگهای کناری هم پوشانی داشته باشند تا در صورت بازی در چاپ این عدم انطباق پوشیده شود که به این تکنیک Traping میگویند.
- خطوط برش، علامتهای انطباق روی ورقه شفاف جهت مونتاژ علامت گذاری شوند که هنگام چسباندن کلیشه، دارای اهمیت زیادی میباشند.
- اگر طرح گرافیکی دارای اشکالی باشد و رنگ بندی آن هم تیره و روشن است، حتماً از تکنیک overprint بهره گرفته شود (Overprint تکنیکی است که در آن شکل تیره بزرگتر از شکل روشن میباشد تا در صورت بازی چاپ لبههای کار روشن بر روی لبههای کار تیره را تلرانس چاپ را بپوشاند).
تاثیر میزان عبور نور
انتخاب دقیق میزان نور برای اینکه تفکیک رنگ به صورت کامل انجام شود خیلی مهم است زیرا هر ضعفی در عبور نور باعث از بین رفتن جزئیات، درخشندگی رنگ در چاپ خواهد شد. شدت نامناسب نور برای تهیه پلیت احتیاج به شرایط خاصی در چاپ و علم کافی به این فرایند دارد که در بیشتر مواقع رعایت نگردیده و باعث چاپ نامطلوب و ضعیف خواهد شد.
تاثیرات فیلم نگاتیو
در فرایند کار با فیلم نگاتیو نیاز است که از فیلم نگاتیو با دانسیته بالا به عنوان ارژینال استفاده کنیم ون برای کیفیت پلیتهای چاپ ضروری است.
در عمل کپی در زمان نوردهی اصلی، فیلم نگاتیو باید بر روی سطح حساس پلی قرار گیرد و هوا بین آنها کاملاً تخلیه شود (وکیوم نامناسب یا باقیماندن هوا بین فیلم و نگاتیو سبب اشکالات زیر میشود):
- از دست دادن ترام های مناطق روشن تصویر در چاپ هافتون
- شارپ و تمیز نبودن قسمتهای برجسته چاپ
- کم شدن جزئیات در چاپ هافتون
- کم شدن عمق بر برجستگیها
- پهن شدن جزئی خطوط به صورت غیرقابل پیشبینی
- مشکل در تنظیم کردن و انطباق کار به خصوص در چاپ هافتون
روتوش کردن
گاهی نیاز است که عناصر تصویر بر روی فیلم نگاتیو اصلاح شود برای این کار میتوان از گل روتوش یا نوار چسب ضد یووی UV (نوار چسب قرمز) استفاده کرد. استفاده از گل روتوش در سمت ژلهای فیلم باعث ایجاد فاصله بین ژلاتین فیلم و سطح حساس پلی در هنگام وکیوم میشود. بنابراین باید از این روتوش در سمت ژلاتین فیلم خودداری کرد.
زمینه آوردن فیلم و سایهدار شدن ترام ها
این اشکالات معمولاً با فرایند نامناسب تولید فیلم نگاتیو باعث میشود در طی کپی فیلم نگاتیو بر روی فوتوپلیمر چاپ، اثر نور یووی ضعیف و محو شود که نیاز به زمان نورردهی طولانیتری دارند. در همان زمان به خاطر نور دهی طولانیتر و بیشتر ترامها لبههای تصاویر محو شده و تاثیر نور uv در مرحله تولید پلیت کم میشود.
حداقل سایز برای عناصر تصویر در چاپ کارتن
در اندازه حروف عناصر تصویر بسته به نوع آنیلوکس( نوع زاویه و per line) مشخص میشود، ولی برای اندازه حروف، پهنای خطوط، بهتر است کمتر از یک میلیمتر نباشد و همچنین اندازه حروف کمتر از فونت ۸ نباشد. اما در چاپ هافتون بسته به نوع آنیلوکس این حروف میتواند کوچکتر نیز شود. البته باید در نظر داشت که ترام جز پارامترهای چاپ فلوکسیوگرافی و به خصوص کارتون میباشد که میتوان در مرحله طراحی و با توجه به نرمافزارهای موجود و آگاهی به نوع و گراماژ کاغذی که در چاپ کارتن مورد استفاده قرار میگیرد مقدار آن را کاهش داد.
کلیشه چاپ کارتن
اجزای تشکیل دهنده فوتوپلیمر عبارتند از:
- عامل اتصال الاستومر : مشخصات فیزیکی کلیشه چاپ از قبیل سختی، قابلیت ارتجاع پذیری و پایداری کلیشه در برابر حلالها مربوط به این جز است.
- منومرها : با توجه به ساختار شیمیایی شان در سرعت پلیمریزاسیون تاثیر داشته و در نتیجه در میزان کم یا زیاد بودن حساسیت به نور پلیت و مقاومت در برابر حلالها نقش دارند.
- آغازگرهای نوری : سرعت پلیمریزاسیون و حساسیت به نور پلیت را کنترل میکنند.
- تثبیت کنندهها : تثبیت کنندههای حرارتی از فرسودگی پلی در طی انبارش و حمل آن از کشور سازنده به چاپخانه جلوگیری میکند.
- افزودنیها : رنگینهها یک نوع افزودنی جهت جذب نور یووی میباشند این افزودنی از بازتابش نور جلوگیری کرده و به کنترل پلیمریزاسیون کمک مینماید از دیگر افزودنیها میتوان به واکسهای رزین که جهت نرم کردن سطح پلیت چاپ استفاده میشود نام برد.
ساختار کلیشه
یک کلیشه از چهار لایه تشکیل شده است:
- پایه پلی استری ز موادی استاتیک شامل ترکیباتی از مونومر ساخته میشود.
- لایه فوتوپلیمری حساس به نور uv ( یووی ).
- لایه پخش کننده نور که باعث رسیدن نور یک دست به پلیمر میشود.
- لایه محافظ که سطح حساس به نور را از آسیبهای فیزیکی و نفوذ اکسیژن حفظ میکند.
ضخامت کلیشه و عمق برجستگی
مناسبترین کلیشههای مورد استفاده در چاپ کارتون برای کارتنهای غیر هافتون ۴.۷ میلیمتر و عمق برجستگی آن ۳ میلیمتر میباشد و برای چاپ هافتون ۳.۱۷ میلیمتر عمق برجستگی آن یک میلیمتر میباشد.
برخی از عواملی که باعث نازکتر شدن کلیشه نسبت به ضخامت اصلی میگردند عبارتند از:
- زمان کافی برای نورردهی نباشد
- دمای حلال شستشوی مناسب نباشد و محلول به صورت کاملاً یک دست مخلوط نشود
- کوتاه کردن زمان ممکن برای شستشو
- خشک نکردن کافی مخصوصاً برای کلیشههای هافتون
عوامل کلیدی پف کردن کلیشه در حین ساخت عبارتند از:
- سیون ناقص بر اساس زمان نوردهی کوتاه یا پایین بودن شدت تابش لامپ
- کم بودن غلظت بوتانول در حلال شستشو
- درجه حرارت بالا و زمان طولانی در مرحله شستشو
سختی کلیشه ( شور )
سختی کلیشه بعد از مرحله پایانی و مرحله نوردهی ثانویه شکل میگیرد که کلیشه دوام نهایی خود را به دست میآورد که این سختی در بقیه عمر کلیشه ثابت باقی میماند. در کلیشههای کارتون، سختی کلیشه بین ۲۵ تا ۲۴ میباشد که برای کارهایی با زمینه گسترده مناسبترین شور بین ۲۵ تا ۲۸ میباشد و برای کارهای ترامپ که فقط شامل نوشتههای ریز میباشد بین ۲۸ تا ۳۵ و برای کارهای هفتم بین ۳۵ تا ۴۲ باشد مناسبتر است.
تولید کلیشه
تولید کلیشه تولید کلیشه شامل ۶ مرحله میباشد که سه مرحله آن فرایند نورردهی میباشد که شامل:
- نوردهی پشت
- نورردهی اصلی
- نورردهی نهایی میباشد
نوردهی از پشت
اولین گام در تهیه کلیشه نور دهی از پشت است که کلیشه بدون فیلم نگاتیو وکیوم و نور دهی میشود. نوردهی از پشت و نورردهی اصلی قبل از مرحله شستشو و نورردهی نهایی در مرحله پایانی صورت میگیرد که اگر مرحله پایانی با نور یووی uv انجام گیرد با مرحله نورردهی نهایی ترکیب میشود نوردهی از پشت و نوردهی اصلی دو مرحله کاملاً متفاوت هستند با این وجود این دو ارتباط نزدیکی با هم دارند و تاثیر زیادی بر روی دوام کلیشه میگذارند. نوردهی مناسب آنقدر اهمیت دارد که محدوده، نورردهی بزرگ، حساسیت بالا و رزولیشن فوق العاده و حتی کوچکترین عناصر در تصویر را به طور صحیح بر روی کلیشه انتقال میدهد.
در صورت رعایت نکات زیر از بروز اشکال جلوگیری خواهد کرد:
- محل ظهور و آمادهسازی فیلم نگاتیو را در صورت امکان از بقیه بخشهای ظهور جدا کنید. اتاق را عاری از گرد و خاک نگه دارید حدالامکان هر روز با آب محل را بشویید.
- در واحد نوردهی، به طور مرتب هر دو سمت روکش و کیوم را با یک پارچه کتان مخصوص تمیز کنید و در صورت نیاز آن را تعویض نمایید.
- واحد نوردهی را تمیز نگه دارید. ذرات ریز گرد و خاک بر روی پوشش ماشین و بر روی لامپ نورردهی وجود دارد ممکن است بر روی روکش وکیوم به کلیشه انتقال داده شود و باید تمیز گردد، به طور مرتب فیلتر گرد و خاک را با هوای فشرده تمیز کنید.
- واحد نوردهی تا حد امکان باید بسته باقی بماند فقط در مواقعی پوشش آن را باز کنید که بخواهید کلیشه را در آن قرار دهید یا بردارید.
- فیلم نگاتیو و پلیت (ورقه پوشش) را به نرمی با پارچه ضد الکتریسیته (Antistatic cloth) ساکن یا قلم موها قبل از نورردهی، خشک کنید، البته تمیز کردن بیش از اندازه نیز باعث ایجاد الکتریسیته ساکن شده و گرد و غبار را به خود میگیرد.
- تمیز کردن باید روی یک میز جدا و خارج از واحد نوردهی انجام گیرد.
- بهتر از ورقه محافظ بر روی کلیشه تا زمان قرار دادن فیلم روی آن باقی بماند.
- اگر در طول آماده سازی وکیوم بخواهید هوای زیر روکش وکیوم را با دست کشیدن خالی نمایید، باید از یک تکه مقوا یا پارچه ضد الکتریسیته ساکن استفاده شود.
- کاملا مراقب باشید که انگشتان شما کثیف نباشد ممکن است که کثیفی به روکش وکیوم انتقال پیدا کرده و در پلیت چاپ ظاهر شود.
هدف از نورردهی از پشت
- بر حساس سازی یشه اثر گذاشته و زمان نورردهی اصلی را کوتاهتر میکند.
- اطمینان از سفت و محکم ترکیب شدن لبههای مشخصات و افزایش دوام کلیشه با ثبات عناصر مشخصات که با نزدیک شدن آنها به زمینه کلیشه صورت میگیرد.
- از میزان چسبندگی بین پایه پلی استری و پایه پلیمری مطمئن شوید.
- ساختن یک زمینه به وسیله پیش پلیمریزاسیون کنترل شده.
- نفوذ پذیری حلال به داخل مواد پلیمری و عمق شستشو با این عمل محدود میشود.
مرحله نورردهی از پشت یکی از مراحل بسیار مهم در تولید کلیشه است. این کار را باید برای همه کلیشهها انجام داد و زمان این کار را باید به وسیله آزمایش به دست آوریم.
اثرات نوردهی از پشت
بعد از اینکه مرحله نورردهی از پشت آغاز میگردد حساسیت سازی به سرعت شروع میشود و اکسیژن که در لایه مونومری در ی انبار کردن کلیشه نفوذ کرده است در لحظه اول بدون ساختن پایه کلیشه مصرف میشود. در اثر نوردهی از پشت قطر زمینه افزایش مییابد بنابراین ارتفاع برجستگیها کاهش مییابد. زمان نوردهی از پشت باید تنظیم شود به این طریق که زمینه دلخواه شامل اختلاف بین عمق برجستگیها و ضخامت کل به طور کامل پلیمریزه شود (polymerized).
نوردهی از پشت صحیح
نوردهی صحیح از پشت تاثیری بر قسمتهای متن و عناصر تصویری در فیلم نگاتیو نمیگذارد. این کار موجب میشود که تا حد امکان عمق شستشو محدود گردد. حتی اگر زمان شستشوی ما خیلی بیشتر از آنکه نیاز از طول بکشد برجستگیهایی که به دست خواهد آمد عمیقتر نخواهد شد. با این وجود زمان شستشو زیادتر از حد ممکن آسیب رساندن به مناطق برجسته کلیشه میشود، بنابراین بهتر است از بالا بردن زمان شستشو پرهیز کرد.
نوردهی از پشت خیلی کوتاه
در این مورد، یک لایه از مواد پلیمری بین سطح پلیمریزه و عناصر برجسته تصویر باقی میماند.
این ممکن است موجب به وجود آمدن عیب و نقص در طی فرایند شستشو گردد. عناصر تصویری ممکن است در مرحله شست و پاک شوند. در این مورد یک لایه ضد پلیمریزه روی سطح زمینه باقی خواهد ماند بعد از مرحله خشک شدن بر روی زمین یک سری برجستگیها و ساختار رگهای مانند، ظاهر خواهد شد.
در این حالت نمیتوانی کلیشه را به طور صحیح شستشو داد و سطوح برجسته را به طور مناسب ایجاد کرد به علاوه ممکن است که مونومرهای باقیمانده روی کلیشه به صورت یک نقص بر روی چاپ ظاهر شود. بنابراین بهتر است قبل از مرحله نوردهی نهایی موبومرها خشک شده و معلق محلول که روی سطح کلیشه ماندهاند، پاک شوند. حساسیت نسبت به نور (photo sensitisation) به دست آمده ناکافی است لذا مرحله نورردهی اصلی طولانیتر خواهد شد. دوام و سختی این نوع پلیها محدود میگردد.
نوردهی از پشت طولانیتر
در کلیشهای که زمینه آن در زمان خیلی طولانی به دست آمده است، عمق برجستگیها به حد مطلوب نمیرسد. متنهای نامطلوب و گاه چسبیده به هم میباشند.
نوردهی اصلی
در نوردهی اصلی (نوردهی تصویر) که همراه با فیلم تحت فشار وکیوم انجام میگیرد، در نوردهی اصلی تصویر به صورت برجسته بر روی تصویر شکل میگیرد. نوردهی یا به صورت تخت یا به صورت دوام انجام میشود. عملیات نوردهی توسط دستگاههایی که مجهز به لامپهای نوری با اشعه یووی میباشند به انجام میرسد. در نوردهی اصلی مناطق برجسته با پلیمریزاسیون مونومرهای پلیت شکل میگیرند. تصویر بر روی سطح پلیت ساخته میشود و مخروطی شکل به سمت پایین در لایههای کلیشه رشد میکند. برخلاف نوردهی از پشت نورردهی اصلی روی سمت امولاسیون کلیشه و با استفاده از فیلم نگاتیو انجام میشود. پس از اینکه ورقه محافظ از روی کلیشه برداشته شد بلافاصله فیلم نگاتیو روی کلیشه قرار میگیرد و به وسیله وکیوم شدن بر روی سطح کلیشه ثابت میشود.
نوردهی مناسب تمام عناصر تصویر را محکم با پایه کلیشه که به وسیله نورردهی از پشت ساخته شده است به سرعت اتصال میدهد.
نوردهی اصلی مورد نیاز بستگی به عوامل مختلف دارد که عبارتند از:
- حساسیت کلیشه خام
- عمق برجستگی مطلوب
- ظرافت عناصر تصویر نگاتیو
پیشنهاد میشود که در دورههای زمانی مختلف شدت اشعه نور یووی را چک کنید زیرا در اثر گذشت زمان از شدت نور خروجی لامپ یووی کاسته خواهد شد.
تاثیر زمان نوردهی اصلی در تراکم تصاویر
زمان نوردهی اصلی باید به اندازه کافی طولانی باشد اما از نوردهی بیش از حد نیاز باید پرهیز کرد. باید عناصر ظریف اصلی تصویر از فیلم نگاتیو به کلیشه انتقال یابد که این عمل تعیین کننده مدت زمان نوردهی است.
اندازههای زیر حداقل اندازههایی است که باید ملاحظه گردد:
- خطوط 0.17 میلیمتر
- نقاط ترامپ 0.25 میلیمتر
- اندازه حروف پنت ۴
- تراکمهای سایه روشن ۲ درصد در ۴۸ خط در سانتیمتر
اگر پیشنهادهای ذکر شده را رعایت کنید عناصر تصویر بدون از دست دادن و چاق شدن یا بولد شدن جزئیات تصویر به طور صحیح به کلیشه منتقل خواهد شد. حتی اگر قرار است عناصر تصویری ظریف تولید گردد ضروری است که شرایط فرایند بهینه سازی شود.
زمان نوردهی بسیار کوتاه
پلیمریزاسیون به پایه نمیرسد و پایه در عناصر تصویر به صورت کامل صورت نمیگیرد. در طی شستشو، پایه عناصر تصویر گرد خواهد شد. خطوط باریک موجدار میشوند و دیگر به هم نمیچسبند. هر ترامپ یا ناحیههای ترامه با ته رنگ کم (سایه روشنها) با فشار شکسته میشود و جزئیات تصویر از بین میرود. سطح برجسته چاپ مثل پوست پرتقال میشود زمان مصرف کلیشه به طور چشمگیری کاهش پیدا میکند.
نوردهی اصلی طولانیتر
نوردهی به اندازه کافی، سبب میشود تمام عناصر تصویری به طور کامل بر روی کلیشه ثبت شود. زمان نوردهی طولانیتر به ویژه بر روی عناصر تصویری فیلم نگاتیو اثر میگذارد. نگاتیو و ترامپهای مناطق سایه را تخت و یا عناصر تصویری نزدیک به یکدیگر میشوند و جزئیات تصویر را از بین میبرد. نوردهی بیشتر سبب میشود وضوح عناصر کلیشه از دست رفته و پرشدگی در ترام و تصویر در طی فرایند چاپ ایجاد شود. هنگام انجام دادن کارهای هافتون چاقی ترام ها افزایش مییابد، تصاویر مات به نظر میرسد و کنتراستها و سایهها بد چاپ میشوند. در حین عملیات چاپ، توجه داشته باشید که کلیشه به تمیز شدن مکرر نیاز دارد.
نتیجه گیری
امیدواریم با مطالعه این نوشتار اطلاعات کافی در خصوص تاثیرات طراحی و ساخت کلیشه در چاپ کارتن بسته بندی را کسب کرده باشید. در اینجا سعی شد تا به کاربردی ترین نکات اشاره و توضیح داده شود. هدف از خلق این صفحه افزایش آگاهی تولید کنندگان کارتن و سفارش دهندگان کارتن جهت بسته بندی کالا می باشد. برای کسب اطلاعات بیشتر میتوانید با کارتن سازی آوین پک در تماس باشید.